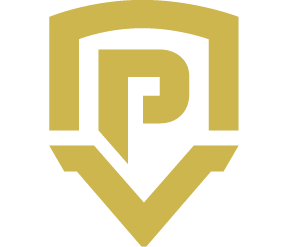
How to Avoid Sourcing Mistakes That Lead to Expensive Downtime
Letâs be honestâno one ever brags about a smooth valve order.
But everyone remembers the one that blew up in their face.
Weâre talking about that one time the wrong valve showed up. Or worseâthe
right one didnât show up at all. And suddenly, your customerâs operation
is stalled, the phoneâs ringing off the hook, and someone wants to know, âWhat
happened?â
Sound familiar? Youâre not alone.
The good news? These headaches are avoidableâwith just a few small shifts
in how you source.
Mistake #1: Ordering Without Real-Time
Availability
Some suppliers will âconfirm stockâ... only to circle back three hours
later with:
âActually, weâre out. Lead time is 3â4 weeks. Hope thatâs okay!â
Itâs not okay. Your customer needed it yesterday.
Fix it: Use suppliers who show real-time availability online. If they
canât give you an instant yes or no, theyâre slowing you downâand putting you
at risk.
Mistake #2: Assuming âClose Enoughâ = Correct Part
Itâs 4:45 PM. Youâve got a customer breathing down your neck. You think the valve you found is the right one⊠but youâre not 100% sure.
You order it anyway.
Two days later:
âThis wonât work. We need the other connection type. Can you expedite a
replacement?â
Yikes.
Fix it: If you're ever even slightly unsure, use suppliers with product
support teams who actually respond quicklyâbonus points if they can confirm
specs live, right on the site or via chat.
Mistake #3: Ordering from Multiple
Sources to Piece It Together
We get the logic. Youâre trying to build a full order from different
vendors because one has this SKU, another has that part⊠and the third might
ship faster.
But managing multiple quotes, tracking multiple shipments, and praying
they all arrive on time? Thatâs a full-time job. And if one piece doesnât show up? Youâre stalled.
Fix it: Streamline your sourcing. Look for suppliers with broad inventory,
fast shipping, and simple checkoutâso you can get it all done in one place.
Bottom Line: Small Mistakes = Big Downtime
Youâre juggling a lotâdeadlines, specs, customer expectations, price
pressure. Itâs easy to slip. But if your sourcing strategy puts speed over
accuracy (or vice versa), itâs only a matter of time before downtime hits.
So if you're looking for a simpler, safer way to source valves,
look for a supplier that gives you:
- Real-time stock updates
- Fast, knowledgeable support
- Easy ordering and returns
Spoiler alert: we built our entire PETROVALVE.COM platform around that.
Because valve sourcing doesnât have to be a gamble.
Ready to skip the stress?
[Check real-time valve availability now] â and avoid your next sourcing
headache before it starts.
âActually, weâre out. Lead time is 3â4 weeks. Hope thatâs okay!â