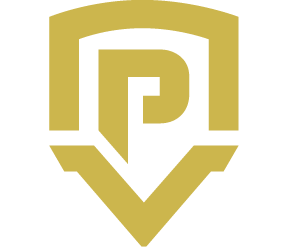
Winterizing Industrial Valves:
A Comprehensive Guide to
Preventive Maintenance in Cold Weather
As the winter season continues, industries relying on
complex machinery face unique challenges in maintaining optimal operational
conditions. One critical aspect that demands attention is the preventive
maintenance of industrial valves.
Cold weather conditions can significantly
impact the performance and longevity of valves, making it essential for
industries to implement comprehensive strategies to winterize their valve
systems. This article provides a detailed guide on preventive maintenance for
industrial valves in cold weather.
1. Understanding the Impact of Cold Weather on Valves:
Extreme cold temperatures can have adverse effects on
industrial valves, potentially leading to issues such as freezing, reduced
flexibility, and increased wear and tear. Understanding how cold weather
impacts valves is crucial for developing an effective preventive maintenance
plan.
2. Insulation and Heat Tracing:
One of the primary measures to protect industrial valves in
cold weather is the use of insulation and heat tracing. Insulating valves helps
maintain a stable operating temperature, preventing freezing and ensuring
smooth operation. Heat tracing involves the use of electrical or steam tracing
systems to provide consistent warmth to valves and associated components.
3. Regular Inspection and Lubrication:
Frequent inspections are paramount in identifying potential
issues before they escalate. In cold weather, valves are susceptible to
corrosion and stiffening of moving parts. Regular lubrication, using
appropriate cold-resistant lubricants, helps ensure that valves operate
smoothly and efficiently.
4. Valve Heating Systems:
For critical applications, the installation of dedicated
valve heating systems can be a proactive approach. These systems utilize
electric or steam heaters to maintain the necessary temperature around valves,
preventing the risk of freezing or damage due to extreme cold.
5. Monitoring and Control Systems:
Implementing advanced monitoring and control systems is
essential for real-time tracking of valve conditions. These systems can detect
temperature variations, pressure fluctuations, and other critical parameters,
allowing operators to respond promptly to potential issues.
6. Emergency Response Planning:
Despite preventive measures, unforeseen circumstances may
arise. Establishing a robust emergency response plan is crucial to minimize
downtime and prevent severe damage. This plan should include procedures for
quickly addressing valve malfunctions and restoring operations to include a
short list of valve suppliers that can provide replacements quickly in the
event of cold weather-related issues.
7. Training and Education:
Ensuring that personnel are well-trained in cold weather
valve maintenance is key to the success of any preventive strategy. Training
programs should cover the identification of potential issues, proper use of
equipment, and emergency response procedures.
Preventive maintenance of industrial valves in cold weather is a critical aspect of ensuring the reliability and efficiency of industrial processes. By implementing insulation, regular inspections, heating systems, and advanced monitoring, industries can minimize the impact of cold weather on their valve systems. A proactive approach, combined with well-trained personnel and effective emergency response planning, will contribute to a smoother operation even in the harshest winter conditions.